AGV Caster Wheels
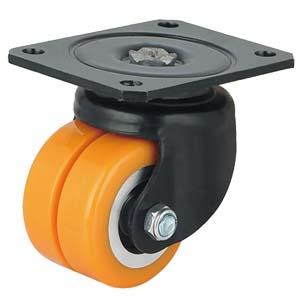
Description:
AGV caster wheelsAluminum alloy core with TPU wheel
Wheel size:Ø55mm,Ø65mm,Ø75mm
Double Ball Bearing
Hardness: 95 Shore A
Work Temperature:-20~70 centi-degree
Why choose our AGV caster wheels
1. The wheel frame adopts double bead plate plane bearing structure, and is formed by heavy-duty steel pressing. And by cold hardening the ball track to achieve a long service life.
2. The steering accuracy of the head is 0.1mm, which ensures the controllability and accuracy of the steering of the AGV casters.
3. The structure of the plane bearing makes the AGV caster wheels steering more flexible, and the dual-wheel differential design greatly improves the flexibility of in-situ steering. We can also equip it with a secondary shock-absorbing spring mechanism to prevent the wheels from hanging and skidding. This can save the power consumption of the AGV battery and extend the working time of the AGV.
4. AGV wheels are made of aluminum core pouring PU, which is light and quiet, suitable for high-speed operation environment, and is often used in the industry of transporting AGV robots
Q: What is an AGV caster and how is it different from a common caster?
A: An AGV caster is a specialized caster designed specifically for use in automated guided vehicles (AGV). These casters are typically made with high-strength materials, such as steel or polyurethane, and are engineered to withstand the demands of high-speed, heavy-load applications.
One key difference between AGV casters and common casters is their level of precision. AGV casters must be extremely precise in order to ensure that the AGV can navigate through a facility without error. This requires careful attention to factors such as load capacity, tread design, and shock absorption.
Another difference is their functionality. AGV casters are designed to work in concert with an AGV, which is a mobile robot that uses sensors and other technology to navigate through a facility. Common casters, on the other hand, are intended for use in manual applications, where they are pushed or pulled by an operator.
Finally, AGV casters often have specialized features that make them suitable for specific types of applications. For example, some AGV casters are equipped with sensors that allow the AGV to detect obstacles and avoid collisions, while others may have high-resistance treads that can withstand exposure to chemicals or extreme temperatures.
Q: What are the benefits of using AGV casters in material handling applications?
A: There are several key benefits to using AGV casters in material handling applications. One of the most significant advantages is increased efficiency. Because AGV can operate continuously 24 hours a day, 7 days a week, without the need for breaks or rest periods, companies can significantly increase their productivity and throughput while also reducing labor costs.
Another benefit is improved safety. With AGV handling the movement of goods, the risk of workplace injuries and accidents is significantly reduced, particularly in facilities where large, heavy loads are being transported.
AGV casters can also offer better flexibility and customization. They can be designed to fit a wide range of different applications and load capacities, allowing them to be used in many different types of facilities. Additionally, they can be equipped with a variety of different sensors and other components to enable them to perform specialized functions, such as navigating around obstacles or avoiding collisions with other robots or equipment.
Q: What factors should be considered when selecting the right AGV caster for a specific application?
A: There are several key factors that should be considered when selecting the right AGV caster for a specific application. These include load capacity, tread design, shock absorption, durability, and compatibility with the AGV system.
Load capacity is a critical consideration, as it determines the weight that the caster is able to support. The caster should be rated to handle the maximum weight that will be transported by the AGV in order to ensure safe and efficient operation.
Tread design is also important, as it affects the caster's ability to grip and maneuver through different types of surfaces. The appropriate tread design will depend on factors such as the type of surface being traversed, the speed of the AGV, and the type of loads being transported.
Shock absorption is another key factor, particularly in facilities where loads are being transported over uneven surfaces or where the AGV is traveling at high speeds. The caster should be designed to absorb shocks and vibrations in order to prevent damage to the AGV or its components.
Durability is also important, as AGV casters must be able to withstand the demands of high-speed, heavy-load applications. They should be constructed with high-strength materials and include features such as reinforced frames and sealed bearings to ensure long-lasting performance.
Finally, compatibility with the AGV system is critical. The caster should be designed to work seamlessly with the AGV and its onboard sensors and other technology in order to ensure safe and efficient operation.
Q: How can AGV casters be maintained in order to ensure optimal performance?
A: Like all casters, AGV casters require regular maintenance in order to ensure optimal performance. This may include tasks such as cleaning, lubrication, and periodic replacement of worn or damaged components.
In addition, it is important to regularly inspect the casters for signs of wear or damage, such as cracks, dents, or uneven tread wear. Any issues should be addressed promptly in order to prevent further damage or potential safety hazards.